Home » Posts tagged 'plastic manufacturing'
Tag Archives: plastic manufacturing
Different Types of Plastic Molding Techniques
American Plastic Molds are the special tool used to make plastic parts and products. They are a vital part of daily hardware, industrial equipment, automobiles and other major applications.
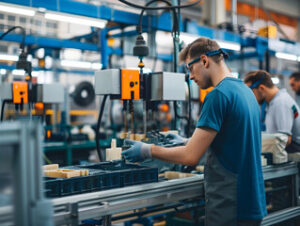
It’s important to understand the process before investing in a plastic injection mold. This way, you can avoid common mold pitfalls that could set your project back weeks or thousands of dollars.
In plastic molding, a polymer such as polyethylene or polypropylene is moulded into a specific shape using heat and pressure. The resulting products are used in the manufacture of a wide range of items, including automotive parts, home appliances, electronics and other industrial goods. There are several different moulding methods for plastics, each offering distinct advantages for certain applications.
Injection molds are the most commonly used type of plastic moulds. They are comprised of a base, injection chamber and ejector mechanism. The base is the structural part that determines the shape of the final product and provides a guide for the injection machine. The injection chamber is where the molten plastic takes its shape, and is surrounded by the ejector mechanism. The ejector mechanism ensures that the finished product is safely removed from the mould without damage. This is achieved by a system of pins and sliders that are activated when the hot plastic enters the mould.
Another common moulding method is blow molding. This involves heating liquid plastic to a soft, almost-putty state before placing it into a heated mold and inflating it to create the desired shape. This technique is effective at producing thin, hollow-walled pieces, such as 2-liter soda bottles or plastic replacements for metal parts.
Rotational molding, or rotomolding, is another common plastic moulding method. This process involves pouring melted plastic into a heated mold, which is then rotated at a high speed. This causes the plastic to evenly coat the walls of the mold, resulting in a hollow-walled product. It is an ideal method for creating large, hollow-walled containers or storage bins. Plastic or metal inserts can be molded into the finished product to create curves, contours and logos, or slots for clips and other accessories.
Rotomoulding
Rotomoulding, also called rotocasting, is an economical method of producing large hollow plastic products. The process involves adding resins into a mould that’s simultaneously heated and rotated both vertically and horizontally. This simultaneous heating and rotation evenly distributes the melted resin and creates uniform wall thickness in the final product. This method is ideal for products that will be exposed to harsh environmental conditions because it can withstand high-impact shocks and stresses.
This method of plastic molding is most commonly used for making plastic replacement parts for existing metal products. It is a low-cost alternative to other methods and offers good thermal stability, making it suitable for outdoor applications.
The liquid plastic is injected into the mold and heated to form a thin film that surrounds it. This coating is a barrier that protects the product from contamination and moisture. It’s then cooled to a solid state before it can be removed from the mould and trimmed of excess material. The resulting plastic products are light and durable, making them ideal for use in construction and other industrial settings.
A plastic injection machine, also known as a moulder or mouldmaker, is used to produce the hollow rotomolded products. It consists of two primary components: the injection mould and the ejector mould. The injection mould seals tightly against the sprue bushing, which is a funnel-shaped metal tube that directs molten plastic to cavity images. The sprue bushing can be fitted with a variety of plastics, including polyethylene and polypropylene.
After the molten plastic has been transferred from the barrel to the mold, it’s time to cool the new product. The cooling stage can take ten minutes and must be carefully controlled to prevent warping. A fan is used to keep the temperature of the plastic below 100°C.
It’s important that the ejector pin is correctly designed to ensure that the plastic is successfully ejected from the upper mould. This is especially important for products with small draft angles and high walls. The ejector pin must be able to apply enough force to overcome the resistance of the product and push it out of the upper mould.
Injection Moulding
Injection molding is one of the most popular methods for making plastic parts. It starts with a raw material in powder or pellet form, which is then heated to high temperatures and injected under pressure into the mold. The injected plastic then cools, taking on the shape of the mold. Once the molded product has cooled, it is removed from the mold. Injection molding is commonly used to make components for automobiles, electronics, home appliances and medical devices.
The first step of injection moulding is to design the mold. This is typically done as a CAD file, which can then be turned into a blueprint for the injection mold. The mold is made by professional machinists who are familiar with the injection molding process. It takes weeks or even months to build an injection mold, and it can cost up to $10,000.
To reduce costs, injection molds are often designed with few cavities. This also helps reduce the amount of time and energy needed to run the injection machine. The number of cavities incorporated into a mold directly correlates to the initial manufacturing costs of the injection mold. In addition, any details that require more complex tooling, such as undercuts or a finer surface finish, will increase the initial cost of the injection mold.
During the injection moulding process, many things can cause defects in the final product. These include dimensional differences, gate marks (where the melt-delivery channels, or sprue and runner, meet the part-forming cavity), and ejector pin marks. These imperfections can result from minute misalignments, wear, gaseous vents, clearances for adjacent parts in relative motion, varying coefficients of thermal expansion between the injection mould components, and non-uniform heating. The skillful injection mould designer can minimize these aesthetic detriments by positioning them where they will not be visible to the consumer, such as in the corners of a part or on internal surfaces.
During the production of an injection molded plastic part, technicians will perform a series of test runs. This is to ensure that the injection process is consistent and accurate. They will start with a small shot weight, and gradually fill the mould until it is 95 to 99% full. The technician/tool setter will then measure the injected plastic mass, and the weight of the molded part. When the weight of the injected plastic remains the same, they will stop injecting material.
Extrusion
Extrusion is a mechanical industrial process where hot melted plastic is forced through a customized die to create a long molded profile that can then be cut into usable lengths. Like injection molding, this versatile method is used to create a broad range of products from pipes and tubing, to food products and 3D printing filaments. However, despite its popularity, this manufacturing technique cannot function without a range of auxiliary equipment.
This specialized equipment includes a series of tools that accept the hot extrudate stream as it exits the die and gradually shape it into a near-finished product. This includes a mandrel, pin or screw that helps form the hollow center of tubular extrusions; a nozzle for creating shaped segments of film and sheet; and an ancillary device that is often used to help spread and distribute the plastic melt evenly across the die face.
The final auxiliary tool in the process is often a cooling unit. This may be a spray or immersion system that transfers heat out of the extrudate as it forms, so it can cool and harden quickly into its finished dimensions. For example, large extrusions like pipe or decking often use water-spray cooling, while smaller flexible tube products benefit from immersion in vacuum-drawn cooling tanks.
When it comes to processing hygroscopic polymers, consistent moisture removal is crucial. This is because internal moisture can cause voids, discoloration and structural weakness in injection molded parts and extruded products. Whether it’s a centralized dryer or multi-hopper drying cart, this auxiliary equipment is essential for any operation that uses hygroscopic materials.
In addition to these specialized tools, an extrusion plant requires an adequate supply of raw materials that can be transformed into the desired end product. The ability to accurately measure the moisture content of this material is also essential. This enables the extrusion process to run smoothly and ensures that the quality of the final product meets or exceeds its target standards. This auxiliary equipment also includes a wide variety of storage and transport solutions to manage the high volumes of raw material required for extrusion operations.